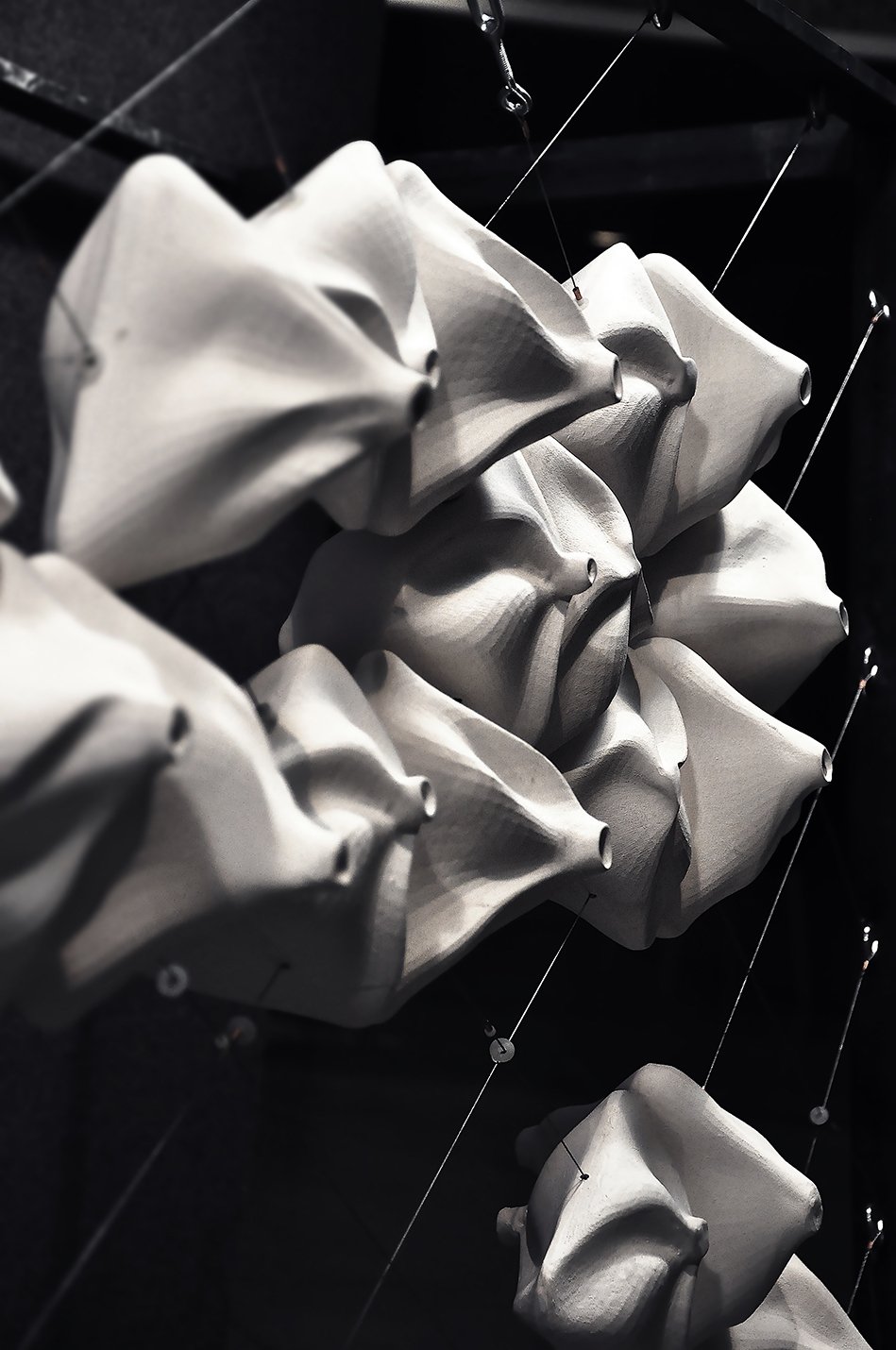
SOUNDSCAPE
Soundscape is an interactive installation that reflects the relationship between sound and form. This wall of ceramic sculptures not only changes in light and shadow, but also makes different sounds when people approach.
2013, at Cornell AAP
Author / Elan Tao, Peter Williamson, Karim Daw and Xueting Wei
Instructor / Jenny Sabin
Keywords / Parametric Design, Ceramic, Interactive Digital
Contribution / Concept development, digital modeling, fabrication, graphical presentation
Design Intention
The theme for this ceramic work was about music, or sound. After researching on the making of ocarina, a simple instrument that can make sound easily, we found that the frequency the wind instrument makes is decided and only decided, by its volume and the length of the nozzle, despite what shape it has. Adopting this idea ceramics can be potentially developed into an interactive installation of generative forms.
Above: ocarina, ceramics that produce sound. From left to right: typical ocarina, factors defining sound frequency, different shapes of ocarina.
Below: Test of making an interactive ceramic piece, ocarina prototype
Design the forms and combinations
Left: the final clay vessel, and also the 3D print mold; Right: the plaster mold
Postive Molds & Negative Molds
Virtual models were made in Maya for flexibility to control the geometry. They were then 3D-printed into positive molds, and using these molds we casted negative molds of plaster. The 3D-print molds had a different mesh texture than the original virtual model, which becomes a trace of digital-fabrication on the ceramics. The size of the component, 7x7 inches, is a size comfortable for people to hold in hand.
Left: 3D-print possitive molds, some broken because of the moisture in plaster; Right: Negative molds in plaster
Clay components out of plaster molds
The size of the component, 7x7 inches, is a size comfortable for people to hold in hand.
Form Development
Since ceramic is efficient for mass production but inefficient for generative, individual designs, the fabrication strategy was important to the project. Traditionally the origami molds are consisted of two halves of plaster molds; so if the joint section is the same, different molds can still be joint together and produce a complete ceramic piece. In that case, we designed the joint section as equilateral triangle which allowed the asymmetrical plaster molds to rotate to 3 different positions during the casting. This meant we could multiple the combination by 3 times. Finally, there were 4 molds of different heights, shapes and nozzle positions. With these molds, we got 30 combinations in total.
Component family
Generating forms
Iterations: (Conbination < 2 out of 4 > + 4)*(360/120)=(4*3/2+4)*3=30
Installation
Our component geometry was triangular in section, and the edges each had a cable hole on its midpoint. These cable holes, created to allow the wire dia-grid to pass through the component, were made after clay casting using a laser cut jig. Furthermore, shrinkage of the ceramics after firing was the major issue that needed to be considered in the final installation, which in our measurements was closer to roughly 8%.
After firing, the ceramic pieces were installed on the grid, and these became an interactive wall of ceramic sculptures, which not only changes in light and shadow, but also makes different sounds when people approach.
Material
3D print plaster molds (positive)
Plaster molds (negative)
White Porcelain Casting Slip - Cone 5
Galvanized Steel Multipurpose Strand Rope, 1 X 7, 1/32” Diameter, 185 Lb Break Strength
Copper Stop Compression Sleeve, For 1/32” Rope Diameter, 1/4” Sleeve Length
Copper Oval Compression Sleeve, For 1/32” Rope Diameter, 1/4” Sleeve Length
Nylon 6/6 General Purpose Flat Washer, Off-white, No. 0 Screw Sz, .18”od, .07”-.09” Thk
Nylon 6/6 General Purpose Flat Washer, Off-white, No. 6 Screw Sz, .44”od, .03”-.05”thk
Open Aluminum Body Turnbuckle, W/zinc-plated Eye & Eye Fittings,5/16”-18 Thread
5/16” White Bumper Post Rings